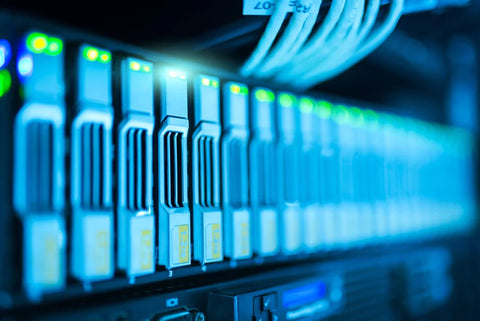
A brief introduction to CAN-bus
What is CAN-bus?
CAN-bus is one of those technologies that everyone experiences every day, without actually knowing about it. Because it is so widely used, in everything from cars and trucks through to boats, factories and even building management systems, the chances of interacting with it on a daily basis are pretty high. But what is CAN-bus and how can it be implemented?
To understand what CAN-bus is, we need to understand why it was created in the first place. Back in the early 1980s cars were becoming more and more complex and the size and complexity of the traditional communications and wiring systems was getting out of hand. To counter this, engineers at Robert Bosch GmbH began development of a serial communications system to allow a more distributed control network and a reduction in the general wiring architecture and complexity. As a result of this development, the first vehicle, a Mercedes S-Class, rolled of the production line with 5 on-board control units communicating over CAN in 1991. Very quickly CAN was adopted in pretty much every engine control system of top-range European vehicles. Since that point CAN has gone on to be the standard in the automotive world and widely used in industrial applications.
The Details
- CAN stands for Controller Area Network
- CAN is a vehicle bus standard designed to allow microcontrollers and devices to communicate with each other in applications without a host computer. It is a message-based protocol, designed originally for multiplex electrical wiring within automobiles, but is also used in many other contexts.
- As an alternative to conventional multi-wire looms, CAN Bus allows various electronic components (such as: electronic control units, microcontrollers, devices, sensors, actuators and other electronic components throughout the vehicle) to communicate on a single or dual-wire network data bus up to 1 Mb/s
- CAN is a multi-master network that uses message priority (arbitration)
- Robust and fault tolerant – designed for high EMC environments (protected by twisted pair and shielding)
- Capable of up to 5KM @ 10kbit/s and as low as 40M @ 1MBit/s (baud rate)
- Internal fault mechanisms (error frames)
- Data exchange between any CAN participants, field devices and process control computers
- System-wide data consistency
- Reduced bus load through data preparation
- Real-time thanks to guaranteed latency time
- Standardised by ISO-11898
What are the benefits of using CAN-bus?
- As a distributed system, it reduces wiring, cost and complexity and enhances overall system capabilities and performance
- Easy integration – because there are so many CAN chip manufacturers who provide the data and physical layer, all the software developer needs to do is to develop the application level code.
- Robust EMC protection - It provides the ability to work in difficult electrical environment and ensures noise free transmission.
- Traffic congestion is eliminated as the messages are transmitted based on their priority and it allows the entire network to meet the timing constraints.
- It provides for error free transmission as each node can check for errors during the transmission of the message and send the error frame.
Implement CAN-communication with Control Technologies UK
So where do we come in? We have over 10 years experience working with CAN and designing and implementing systems with it. From agriculture, via ground support equipment to electric vehicles and trains, we've worked on some pretty complex applications. Through our work with CAN we've learned what does and doesn't work and are able to work closely with our customers to ensure that CAN is applied correctly or assist when things aren't quite right. We've work with a wide range of hardware partners and we are extremely capable of implementing CAN in all it's forms.
If you are embarking on CAN implementation, tasked with supporting an existing CAN system or looking for someone to develop a complete end-to-end solution, we can help. If you're looking for a complete solution we offer a no-obligation 2 hour workshop with your key personnel to explain the benefits and technology behind CAN, understand your requirements and discuss possible solutions. If you want to know more, please get in contact.